December 5, 2008 — How do you build the tires for a car that can drive on the moon?
That was the question that NASA asked — and Goodyear answered — in the 1960s with the Apollo Lunar Roving Vehicle (LRV) wire mesh tire. Forty years later, the space agency and rubber company have partnered to answer a similar question: How did they build the moon rover tires?
Duplicate dozen
Goodyear and NASA's Glenn Research Center (GRC) in Cleveland, Ohio recently completed a project to develop and produce 12 replicas of the original tire used on the Apollo LRV. The jointly-funded effort was intended as a first step towards understanding the tire's non-pneumatic design and the applications it has, both on the moon and the Earth.
Duplicating the dozen tires was less a question of form as it was of function.
"Although there was some reference material for designing the replicate tire, there was little detail about the manufacturing process," said Goodyear's project leader Rick Laske.
The team examined one of the moon tires on display at the National Air and Space Museum in Washington, D.C., and corresponded with two retired members of the Apollo Lunar Roving Vehicle team, each of whom had a tire that had been given to them as a souvenir for their work. The inspection of the original tires became the primary means for judging the quality of the replicas.
Anatomy of a moon tire, and its replica
"The basic rubber-pneumatic design used on Earth does not have the same utility on the moon," explained Vivake Asnani, NASA's principal investigator. "Lunar tires need to be designed to develop traction on sandy undulated terrain, in regions that humans have never even seen up close."
"Plus, the prospect of an immobilizing 'flat tire' would be devastating to the mission," added Asnani.
Four major components comprised the LRV tire's design: mesh, tread, inner-frame and hub.
The mesh was woven out of piano wire to provide a soft, springy surface to contour to the ground and provide good ride quality. The tread was made from a series of metal strips intended to protect the mesh from impact while providing increased contact area for floatation in soft soil.
The inner-frame, comprised of a relatively rigid metal structure, prevented the mesh from over-deforming during impact, while the hub held the mesh and frame together as well as connected the wheel assembly to the rover.
"Before the wire mesh could be woven, 3,000 feet of wire had to be custom-crimped and cut into 800 pieces," said Laske in a statement issued this week by Goodyear.
A hand loom was designed to weave the crimped wires into a rectangle measuring approximately 100 inches long and 25 inches wide. Each end of the rectangular weave was then interlaced by hand to form a cylinder, such that it behaved similarly to a child's finger trap puzzle, lengthening and shortening with changes to its diameter.
Sides of the mesh cylinder were pulled down and clamped to a circular jig, roughly the size of a wheel hub, to give the mesh the shape of a tire. Then the jig and mesh were baked in an industrial oven to relieve residual stress from the wire.
The end result was a tire that looked like the skeleton of an Earth tire. The approach worked because each tire was only required to support about 60 pounds of weight (on the moon, the equivalent of 360 pounds on Earth) and be used for a maximum of 75 miles.
Model for the future
As NASA prepares to return to the moon, a new fleet of lunar vehicles will require tires to support about 10 times the weight and last for up to 100 times the distance of the original moon buggy.
To extend the utility of the wire mesh tire, NASA and Goodyear plans tests to find out how and why their load and life are limited. Essentially, the tires will be loaded and cycled until they fail.
To insure the tests are accurate, the replica tires were evaluated for geometry, stiffness and other performance factors, and compared against data from the two moon tire artifacts, as well as limited measurements taken in the 1960s.
"The measurements indicate that the original and replicate wire mesh moon tires have nearly identical mechanical properties," confirmed Asnani. "We are now testing the replicates to determine their traction and endurance capabilities. These data will enable NASA and industry to determine possible applications for the wire mesh tire."
"Not only will the outcome of this project deliver a product that can handle the performance capabilities required for lunar mobility and beyond, we expect the outcome will yield answers to how future non-pneumatic tires may be designed for Earth applications," said Dave Glemming, Goodyear's principal investigator.
"There was great synergy in this project, and we are continuing our collaboration to mature this technology," Asnani added. |
|

Retracing their tracks: NASA and Goodyear worked together to recreate the Apollo Lunar Roving Vehicle (LRV) tire. (Goodyear)
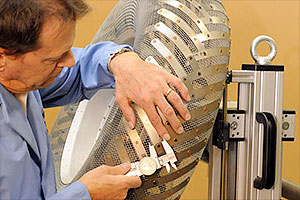
Goodyear's project leader Rick Laske checks tread plate widths of the wire-mesh structure. (Goodyear)
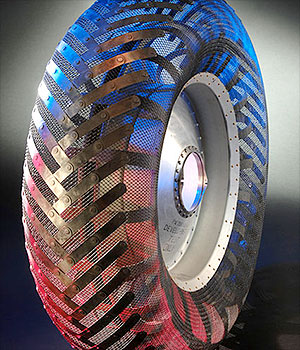
A replica of the Apollo Lunar Roving Vehicle (LRV) tire. (Goodyear)
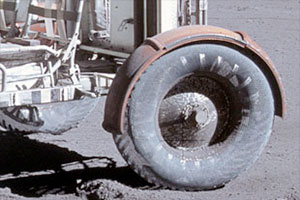
The Apollo 15 Lunar Roving Vehicle (LRV) on the moon. (NASA) |