|
|
Author
|
Topic: Orion crew module ground test article
|
Robert Pearlman Editor Posts: 50516 From: Houston, TX Registered: Nov 1999
|
posted 07-10-2010 10:50 AM
Lockheed Martin release (June 15, 2010) Orion Spacecraft Takes ShapeLockheed Martin Completes Final Friction Stir Weld on Orion Spacecraft The Orion crew exploration vehicle took shape as the two halves of the crew module were fused together at NASA's Michoud Assembly Facility in New Orleans, La. The Lockheed Martin Orion team welded the forward cone assembly to the aft barrel assembly using the next generation friction stir weld process. The 445-inch long weld is the longest such weld of its kind and will ensure optimal structural integrity for the harsh environments of space flight. The completion of the crew module welds marked another key milestone for the Orion crew exploration vehicle, completing the structural framework of the spacecraft. All welds have met stringent quality requirements without any rework required. Prior to flight testing, this crew module will be tested on the ground in flight-like environments, including static vibration, acoustic, and water landing tests. Results will be used to correlate sizing models for all subsystems on the vehicle. Orion weld operations take place on a Universal Weld System II (UWS II) that includes a 22-foot diameter turntable, a self-reacting friction stir weld head and a modular t-grid floor. The system affords virtually unlimited five-axis welding on fixture-mounted hardware. The UWS II is part of the National Center for Advanced Manufacturing, managed by the University of New Orleans Foundation in partnership with NASA and the State of Louisiana. The friction stir welding process advances the state-of-the-art for circumferential welds, yielding higher strength and higher quality welds at a lower cost. The latest state-of-the-art manufacturing technologies, efficient processes and new materials, such as the ultra-light weight Aluminum-Lithium alloy, are all being employed on Orion to produce the lightest possible vehicle for space flight. "The combination of material and manufacturing advancements in technology are key reasons why the spacecraft is more lightweight and damage resistant than many industry experts thought possible," said Larry Price, Lockheed Martin Orion deputy program manager. "The balance of manufacturing methods and varied materials such as composites and advanced alloys that have been applied to Orion resulted in vehicle optimizations across the board - lowest cost, lightest weight, and improved structural integrity, which is critical to crew safety." Lockheed Martin is the prime contractor to NASA for the Orion crew exploration vehicle - the nation's next generation spacecraft for future exploration throughout our solar system. The Orion spacecraft is comprised of a crew module for crew and cargo transport; a service module for propulsion, electrical power and fluids storage; a spacecraft adapter for securing it to the launch vehicle, and a launch abort system that will significantly improve crew safety. |
Robert Pearlman Editor Posts: 50516 From: Houston, TX Registered: Nov 1999
|
posted 09-02-2010 05:32 PM
Lockheed Martin release Orion Performs Under PressureThe Lockheed Martin Orion team performed well under pressure as the first Orion spacecraft successfully passed a structural proof pressure test at the NASA/Michoud Assembly Facility in New Orleans, La., on Aug. 30, 2010, paving the way for future tests prior to space flight. This Orion spacecraft will be used for ground and flight test operations to correlate test data with analytical models to validate Orion's flight design engineering. Built to spaceflight specifications, the vehicle completed an important series of leak and proof pressure tests that confirmed Orion's structural design can withstand long-duration missions. The test incrementally pressurized the spacecraft with breathing air up to 15.55 pounds per square inch - or 1.05 atmospheres -- which is the equivalent pressure a scuba diver's gauge would read at a 35-foot depth. Pressure Proof: An overhead view of the Orion spacecraft after completion of a series of structural integrity tests at NASA's Michoud Assembly Facility in New Orleans. The successful tests demonstrated a leak-free structure fabricated using self-reacting friction stir welding techniques, a technology that produces stronger and higher quality joints when compared with conventional welding. The pressurization test demonstrated weld strength capability, and advanced aluminum-lithium alloy structural performance at maximum flight operating pressures, making this structure survivable in the harshest environments of space. Test engineers monitored and collected data from 600 channels of instrumentation to support margin assessments and confirm design accuracy. Successful test completion allows the hardware to advance to subsystem assembly and integration. Following additional testing in 2010, the assembled crew module will be mated to the launch abort system to undergo ground tests in flight-like environments in 2011. All testing was accomplished at the NASA Michoud Assembly Facility, leveraging advanced technology and a diverse workforce experienced in all of NASA's human spaceflight programs. Recent engineering graduates supporting the Lockheed Martin team gained hands-on experience by designing elements of the successfully tested Orion spacecraft. |
Robert Pearlman Editor Posts: 50516 From: Houston, TX Registered: Nov 1999
|
posted 02-10-2011 08:09 AM
Lockheed Martin release Lockheed Martin Ships Out First Orion SpacecraftThe Lockheed Martin Orion team shipped out the first Orion crew module spacecraft structure today from NASA's Michoud Assembly Facility in New Orleans, La. The spacecraft is headed to Lockheed Martin's Denver, Colo., facilities where it will undergo a series of rigorous tests to confirm Orion's ability to safely fly astronauts through all the harsh environments of deep space exploration missions. 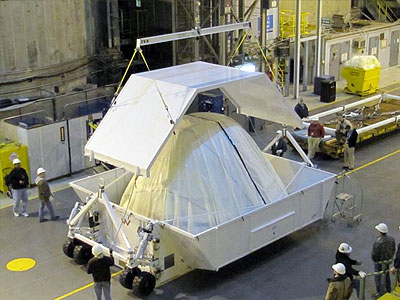 Soon after the spacecraft arrives in Denver, it will be integrated with the heat shield and thermal protection backshell before undergoing environmental testing. This crew module will also go through a series of simulated landing scenarios at Langley's new Hydro Impact Basin. The Langley facility will be used to test, validate and certify water landings for all human-rated spacecraft for NASA. "This is a significant milestone for the Orion project and puts us on the right path toward achieving the President's objective of Orion's first crewed mission by 2016," said Cleon Lacefield, Lockheed Martin vice president and Orion program manager. "Orion's upcoming performance tests will demonstrate how the spacecraft meets the challenges of deep-space mission environments such as ascent, launch abort, on-orbit operations, high-speed return trajectory, parachute deployment, and water landings in a variety of sea states." Built to spaceflight specifications, this Orion ground test vehicle has already validated advanced production processes, equipment and tools required to manufacture the Orion crew module space flight hardware. Data collected from the testing and pathfinding operations will be incorporated to enhance design, requirements, tooling, processes, inspection and test that will ultimately result in a safe, reliable and affordable human-rated space exploration vehicle. 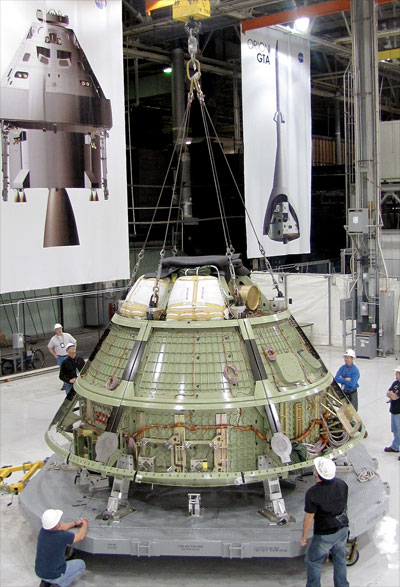 Above: Lockheed Martin's Orion team at NASA's Michoud Assembly Facility in New Orleans, La., inspects the Orion crew module ground test structure prior to shipping. Orion has passed critical human-rating milestones, including Orion's flawless flight test of its launch abort system and the successful phase one safety review that validated Orion meets many of NASA's stringent requirements for safe human spaceflight. Lockheed Martin is the prime contractor to NASA for the Orion crew exploration vehicle - the nation's next generation spacecraft that features advanced technologies for more complex and challenging human space exploration missions throughout our solar system. The Orion spacecraft will be comprised of a crew module for crew and cargo transport; a service module for propulsion, electrical power and fluids storage; a spacecraft adapter for securing it to a launch vehicle, and a launch abort system that will significantly improve crew safety. | |
Contact Us | The Source for Space History & Artifacts
Copyright 2023 collectSPACE.com All rights reserved.

Ultimate Bulletin Board 5.47a
|
|
|
advertisement
|