|
|
Author
|
Topic: NASA's Orion MPCV heat shield development
|
Robert Pearlman Editor Posts: 50516 From: Houston, TX Registered: Nov 1999
|
posted 09-15-2006 08:51 PM
NASA release NASA Awards Thermal Protection Contract for Orion SpacecraftNASA has selected The Boeing Company, Huntington Beach, Calif., to support the design and development of a lunar direct return-capable heat shield for the Orion crew exploration vehicle. The hybrid firm fixed-price and cost-plus-fixed-fee contract has a 16-month period of performance, with a maximum value of approximately $14 million, including all priced options. The heat shield will protect the spacecraft and crew during atmospheric reentry following missions to the moon or the International Space Station. The heat shield attached at the base of the spacecraft will reject the majority of the heat generated during re-entry into Earth's atmosphere. Returning from missions to the station, Orion will re-enter at speeds similar to those experienced by the space shuttle - 16,700 miles an hour. Returning from the moon, Orion will reenter the atmosphere at speeds of about 25,000 miles an hour and experience heating about five times as extreme as missions returning from the station. NASA's Constellation Program is developing Orion as NASA's primary vehicle for future human space exploration. Orion will carry astronauts to the station by 2014, with a goal of landing astronauts on the moon no later than 2020. The present Phase II contract with Boeing is a continuation of an earlier Phase I NASA effort that evaluated phenolic impregnated carbon ablator (PICA), as well as four other candidate materials using extensive testing and analysis. Boeing has been selected to provide PICA, a proprietary material manufactured by its subcontractor, Fiber Materials Inc. of Biddeford, Maine, for continued testing and evaluation. Boeing's deliverables for this contract include: - Samples of thermal protection system materials for thermal, structural and environmental testing and analysis
- A preliminary heat shield design and detailed heat shield implementation plan using PICA
- A full-scale 16.5-foot (5-meter) heat shield manufacturing demonstration unit
- Comprehensive trade studies targeted toward increasing the technology readiness of a PICA-based heat shield.
- A material properties database and thermal response model for PICA
NASA's Ames Research Center, Moffett Field, Calif., is the agency's lead center for thermal protection systems and will use its thermal, structural and environmental facilities to conduct extensive testing and evaluation of the PICA deliverables. Ames will assess the material performance and its risks and suitability for use as the Orion heat shield. NASA will work with Boeing to provide key validation and verification functions, as well as contributing toward the development and delivery of the overall preliminary heat shield design. |
Robert Pearlman Editor Posts: 50516 From: Houston, TX Registered: Nov 1999
|
posted 05-05-2007 01:16 AM
NASA release NASA Awards Heat Shield Material Contracts for Orion SpacecraftNASA has selected The Boeing Company, Huntington Beach, Calif., and Textron Systems, Wilmington, Mass., to develop alternate heat shield materials for the Orion crew exploration spacecraft. The two contracts for Alternate Block 2 Thermal Protection System (TPS) Materials and Heat Shield Systems Advanced Development will support development and testing of three alternative heat shield materials, designs and manufacturing processes. Under the contracts, the companies will work to ensure the technologies are mature enough to become viable backups if there are difficulties with the primary material. NASA's Constellation Program is developing Orion as America's primary vehicle for future human space exploration. Orion will carry astronauts to the International Space Station by 2015, with a goal of landing astronauts on the moon no later than 2020. The Orion TPS Advanced Development Project, led by Ames Research Center, Moffett Field, Calif., was established to develop a heat shield to protect Orion during its return from low-Earth orbit or the moon. In September 2006, Boeing was awarded a contract to develop the primary heat shield material, Phenolic Impregnated Carbon Ablator (PICA), manufactured by its subcontractor, Fiber Materials, Inc., Biddeford, Maine. The alternate materials will be developed fully only if the primary material does not perform to Orion Project specifications. NASA will assess and evaluate all of the Alternate Block 2 TPS materials through initial testing and select the most promising of the materials for further development, if needed. The Alternate Block 2 contract awarded to Boeing has an approximate value of $10 million, including all options, and calls for Boeing to perform early investigation of a proprietary material, the Boeing Phenolic Ablator (BPA). The contract awarded to Textron has a value of approximately $24 million, including all options, and calls for Textron Systems to perform early investigation of two proprietary material options, Avcoat (used on Apollo) and Dual Layer. Each contract has a 16-month performance period from May 4, 2007, until Aug. 31, 2008. |
Robert Pearlman Editor Posts: 50516 From: Houston, TX Registered: Nov 1999
|
posted 11-19-2007 12:05 AM
Boeing release Boeing completes prototype heat shield for NASA Orion spacecraftBoeing has completed a developmental heat shield for NASA's Orion Crew Exploration Vehicle (CEV) that is designed to protect future astronauts from extreme heat during re-entry into Earth's atmosphere following lunar and low-Earth orbit missions. NASA Ames Research Center last year awarded Boeing Advanced Systems a contract to deliver a Thermal Protection System (TPS) Manufacturing Demonstration Unit (MDU) for the Orion capsule as part of NASA's Constellation program to return humans to the moon and on to Mars. 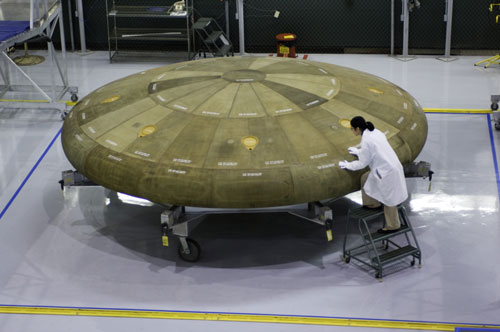 "Boeing took on the challenge of engineering, fabricating and assembling the largest ablative heat shield ever constructed," said Thomas Andrews, Boeing Thermal Protection System program manager. "Our Manufacturing Demonstration Unit met NASA's Advanced Development Program risk reduction objectives to move the Orion heat shield program toward full-scale development in preparation for CEV missions." Development of the five-meter wide TPS MDU began in late 2006 at Boeing in Huntington Beach, Calif. Last month, a NASA Ames technical and quality inspection team successfully completed an acceptance review of the unit. Boeing today shipped the TPS MDU to NASA's Kennedy Space Center in Florida where it will undergo additional inspection. "The successful completion of this new heat shield is a major achievement by our TPS team," said Alex Lopez, Boeing vice president of Advanced Network and Space Systems. "Boeing has greatly improved upon TPS design, analysis and production to meet the harsh environments of lunar return missions. We have the processes, tools and capabilities to successfully produce reliable heat shields for Orion missions. Once again, Boeing is proud to be supporting NASA's space exploration efforts." Boeing's baseline TPS is fabricated from Phenolic Impregnated Carbon Ablator (PICA) material. Fiber Materials Inc., of Biddeford, Maine, produces the material under a contract to Boeing. PICA is being considered for Orion's heat shield due to its proven performance on NASA's Stardust spacecraft heat shield. The Boeing TPS MDU consists of an integrated concept made up of multiple PICA components. Each piece is significantly larger than typical space shuttle tiles, greatly reducing parts count and complexity. Boeing installed the TPS MDU onto a NASA-provided surrogate carrier structure representing the size and shape of the flight heat shield structure, but fabricated from alternate materials pending development of the final flight structure. In addition to the TPS MDU, Boeing has provided NASA other Orion-related hardware including hundreds of arc jet test coupons (sample pieces of PICA and other materials for extreme heat testing), structural and environmental test assemblies, and Local Design Demonstration Units representing structural and thermal protection components of the system that joins Orion's Crew and Service Module elements. Boeing is continuing its work with NASA Ames to develop the flight heat shield design in support of Orion's TPS preliminary design review in early 2008. |
Robert Pearlman Editor Posts: 50516 From: Houston, TX Registered: Nov 1999
|
posted 11-29-2007 08:23 PM
In Hangar N at NASA's Kennedy Space Center, a heatshield for the Constellation crew exploration vehicle Orion was prepared for a demonstration on November 27. 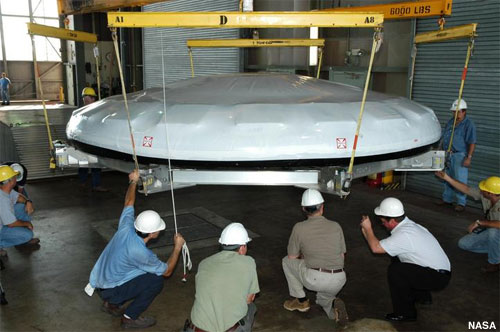 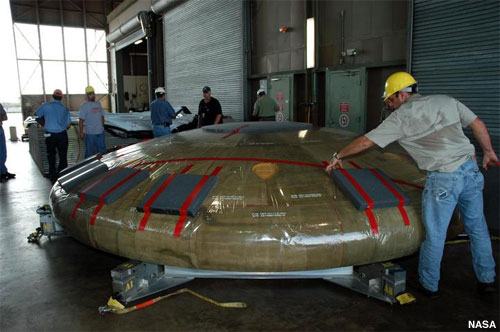
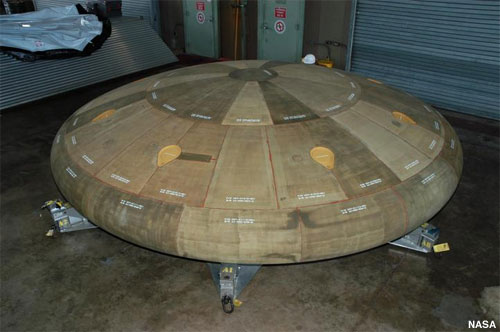 |
Robert Pearlman Editor Posts: 50516 From: Houston, TX Registered: Nov 1999
|
posted 04-07-2009 02:40 PM
NASA release NASA Selects Material for Orion Spacecraft Heat ShieldNASA has chosen the material for a heat shield that will protect a new generation of space explorers when they return from the moon. After extensive study, NASA has selected the Avcoat ablator system for the Orion crew module. Orion is part of the Constellation Program that is developing the country's next-generation spacecraft system for human exploration of the moon and further destinations in the solar system. The Orion crew module, which will launch atop an Ares I rocket, is targeted to begin carrying astronauts to the International Space Station in 2015 and to the moon in 2020. Orion will face extreme conditions during its voyage to the moon and on the journey home. On the blistering return through Earth's atmosphere, the module will encounter temperatures as high as 5,000 degrees Fahrenheit. Heating rates may be up to five times more extreme than rates for missions returning from the International Space Station. Orion's heat shield, the dish-shaped thermal protection system at the base of the spacecraft, will endure the most heat and will erode, or "ablate," in a controlled fashion, transporting heat away from the crew module during its descent through the atmosphere. To protect the spacecraft and its crew from such severe conditions, the Orion Project Office at NASA's Johnson Space Center in Houston identified a team to develop the thermal protection system, or TPS, heat shield. For more than three years, NASA's Orion Thermal Protection System Advanced Development Project considered eight different candidate materials, including the two final candidates, Avcoat and Phenolic Impregnated Carbon Ablator, or PICA, both of which have proven successful in previous space missions. Avcoat was used for the Apollo capsule heat shield and on select regions of the space shuttle orbiter in its earliest flights. It was put back into production for the study. It is made of silica fibers with an epoxy-novalic resin filled in a fiberglass-phenolic honeycomb and is manufactured directly onto the heat shield substructure and attached as a unit to the crew module during spacecraft assembly. PICA, which is manufactured in blocks and attached to the vehicle after fabrication, was used on Stardust, NASA's first robotic space mission dedicated solely to exploring a comet, and the first sample return mission since Apollo. "NASA made a significant technology development effort, conducted thousands of tests, and tapped into the facilities, talents and resources across the agency to understand how these materials would perform on Orion's five-meter wide heat shield," said James Reuther, the project manager of the study at NASA's Ames Research Center at Moffett Field, Calif. "We manufactured full-scale demonstrations to prove they could be efficiently and reliably produced for Orion." Ames led the study in cooperation with experts from across the agency. Engineers performed rigorous thermal, structural and environmental testing on both candidate materials. The team then compared the materials based on mass, thermal and structural performance, life cycle costs, manufacturability, reliability and certification challenges. NASA, working with Orion prime contractor Lockheed Martin, recommended Avcoat as the more robust, reliable and mature system. "The biggest challenge with Avcoat has been reviving the technology to manufacture the material such that its performance is similar to what was demonstrated during the Apollo missions," said John Kowal, Orion's thermal protection system manager at Johnson. "Once that had been accomplished, the system evaluations clearly indicated that Avcoat was the preferred system." In partnership with the material subcontractor, Textron Defense Systems of Wilmington, Mass., Lockheed Martin will continue development of the material for Orion. While Avcoat was selected as the better of the two candidates, more research is needed to integrate it completely into Orion's design. 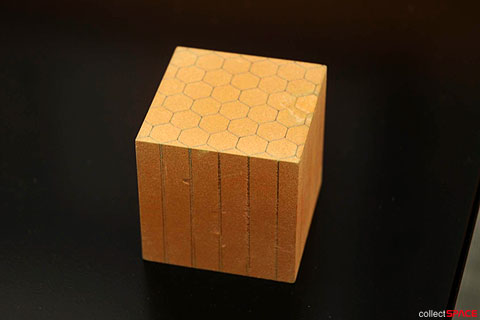 Avcoat heat shield sample produced for NASA's Orion spacecraft |
SpaceAholic Member Posts: 5246 From: Sierra Vista, Arizona Registered: Nov 1999
|
posted 04-07-2009 03:37 PM
Old is new and new is old!Any word on whether a specific formulation has been nailed down? 5026-39HCG was used on the Apollo command module... will be interesting to see if NASA tinkers a bit with the recipe to try an make it better or if the perfection achieved 40 plus years ago persists to this day. |
Robert Pearlman Editor Posts: 50516 From: Houston, TX Registered: Nov 1999
|
posted 04-07-2009 03:47 PM
As the release hints, the formulation is different, because they are no longer able — physically and legally — to produce the original blend. Otherwise, the modern Avcoat was created to be as similar to its Apollo-era predecessor as possible.According to NASA, the modern Avcoat is proprietary, so details of its consistency may not be readily available. |
SpaceAholic Member Posts: 5246 From: Sierra Vista, Arizona Registered: Nov 1999
|
posted 04-07-2009 04:16 PM
I know firsthand there has been difficulty securing original Avcoat because I received a call and email in October from SRI to release my one foot block for tomography and destructive testing.Non-destructive testing is one thing but having the artifact irrevocably converted to plasma didn't appeal to me so respectfully declined. |
NovaRob Member Posts: 242 From: Tucson, Arizona, USA Registered: Nov 2008
|
posted 04-08-2009 03:11 PM
quote: Originally posted by Robert Pearlman: no longer able – physically and legally – to produce the original
Is that because of hazardous materials/processes in the original, or unavailable materials, or proprietary to someone else? |
SpaceAholic Member Posts: 5246 From: Sierra Vista, Arizona Registered: Nov 1999
|
posted 04-08-2009 04:04 PM
Avco produced the original material. They were acquired by Textron who was awarded the contract on the Orion thermal protection system. So unless the original patent was sold off by AVCO I don't believe there would be a legal impediment to its production. My guess is given the initial low quantities required for testing and evaluation, it was cost prohibitive to implement the regime necessary for compliance with existing environmental regulations. How Ames and Langley got around that would be a good question for their TPS guys but it probably involved scavenging pre-existing samples (as noted above) and maybe having Textron temporarily provide an analog formulation which closely mirrored the original 5026-39. |
Robert Pearlman Editor Posts: 50516 From: Houston, TX Registered: Nov 1999
|
posted 03-02-2010 11:22 AM
Lockheed Martin release Lockheed Martin Orion Team Fabricates World's Largest Heat Shield StructureThe Lockheed Martin-led team developing the Orion crew exploration vehicle achieved a major technology milestone by completing fabrication of the world's largest heat shield structure. The shield is five meters (16.4 feet) in diameter and is critical to the protection of the spacecraft and its crew from the extreme temperatures experienced during re-entry. The work was completed at Lockheed Martin's composite development facility in Denver, Colo. 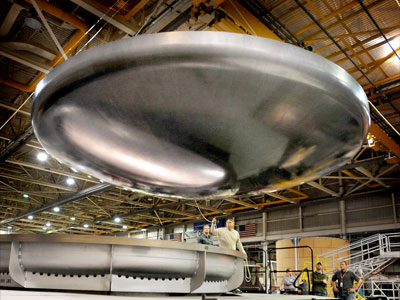 Credit: Lockheed MartinThe crew exploration vehicle is at the height of its development phase, which has spurred several new technologies and innovations such as a cutting edge high-temperature composite material system. The new system was developed by the Lockheed Martin Orion thermal protection system team in partnership with TenCate Advanced Composites, a leading supplier of aerospace thermoset and thermoplastic prepregs. TenCate's composite materials are used in commercial aircraft, radomes, satellites, general aviation, oil and gas, medical and high-end industrial applications. "In addition to the technology advancement, we achieved a $10 million cost savings and improved the project schedule by 12 months through the innovative tooling, materials and fabrication processes the team put into action," explained Cleon Lacefield, Lockheed Martin vice president and Orion program manager. The new resin system was developed over an 18-month period during which thousands of coupons were tested in extreme environments that simulated a ballistic re-entry from a lunar mission. The team verified that the thermal insulator on the outside of the composite material can be thinner due to the higher temperature capability, resulting in improved mass optimization of the Orion spacecraft. The new resin system enables much simpler and more efficient manufacturing techniques compared to other high temperature resin systems. This resin system has the potential to be used in a wide range of commercial applications including aircraft, automobiles, launch vehicles, payload fairings, and re-entry vehicles. The expansive heat shield will be applied to the Orion ground test article, which is the first full-sized, flight-like test article for Orion being built at the Michoud Assembly Facility in New Orleans, La. The ground test article is designed to serve as a production pathfinder to validate the flight vehicle production processes and tools. When completed, the crew module will be tested on the ground in equivalent flight-like environments, including static vibration, acoustics and water landing loads. This early high fidelity testing is necessary to correlate sizing models for all subsystems on the vehicle. |
SpaceAholic Member Posts: 5246 From: Sierra Vista, Arizona Registered: Nov 1999
|
posted 03-02-2010 11:41 AM
The above article suggest that something other then 5026-39 is being employed (at least for the lower heat shield) since Avcoat is technically not a composite. If true Lockheed must have revisited (with NASA) the original decision to go with a heritage TPS ablator. |
Robert Pearlman Editor Posts: 50516 From: Houston, TX Registered: Nov 1999
|
posted 07-17-2013 10:46 AM
NASA video release Orion's Heat Shield Takes ShapeTechnicians at Textron Defense Systems near Boston are applying Avcoat ablator material to some 330,000 cells of a honeycomb on the heat shield of NASA's new Orion spacecraft. To ensure that each cell is filled correctly, they are individually X-rayed and a robot is used to machine the material, sanding off fractions of an inch so that the heat shield matches Orion's precise plans. |
SpaceAholic Member Posts: 5246 From: Sierra Vista, Arizona Registered: Nov 1999
|
posted 07-17-2013 11:36 AM
Take away the robots, add AVCO patches to the back of the technicians lab coats and we would be watching the production of an Apollo heatshield. |
David Carey Member Posts: 989 From: Registered: Mar 2009
|
posted 07-17-2013 02:08 PM
...except they didn't have iPods back then to jam down with while individually hand-loading ALL those hex-cells. (Perhaps they are just ear-bud-looking hearing protection or something but filler #2 seems to have some tunes going on.) I know voiding is a key concern but can't believe a (semi-)automated fill process hasn't been devised over all these years. Fun to watch though.... | |
Contact Us | The Source for Space History & Artifacts
Copyright 2023 collectSPACE.com All rights reserved.

Ultimate Bulletin Board 5.47a
|
|
|
advertisement
|