Author
|
Topic: My personal Apollo story (Dan Schaiewitz)
|
MCroft04 Member Posts: 1861 From: Smithfield, Me, USA Registered: Mar 2005
|
posted 09-18-2017 08:29 PM
quote: Originally posted by Daniel on the Moon: ...I found a few of the many specific references to Apollo 11 astronauts Armstrong and Aldrin.
Four references to the two astronauts and in three of them Buzz's name is first. Any logic to this? |
Daniel on the Moon Member Posts: 354 From: Bronxville, NY Registered: Jun 2015
|
posted 09-18-2017 10:48 PM
It's funny you mentioned this. This is the first time since 1969 that I looked at my log books and I also questioned myself as to the logic?I also noticed that the two mentions of Apollo 11 backup astronauts Lovell and Haise were, you guessed it, Haise and Lovell! Perhaps I was thinking in terms of alphabetical order! |
Daniel on the Moon Member Posts: 354 From: Bronxville, NY Registered: Jun 2015
|
posted 09-19-2017 07:24 PM
The PLSS/OPS was, of course, designed to be functionally operational on the moon. However, as I've discussed previously, using the lunar designed PLSS/OPS for Apollo KSC EVA crew training was a "non-starter." As a result of not being able to use a lunar designed PLSS/OPS, we developed several pieces of hardware to emulate all the functional aspects of the PLSS/OPS in order to successfully carry out the Apollo mission EVA crew training requirements.The key component hardware required were the cryopack, the airpack, the addition of a water cooling device for both the cryopack and airpack (when conditions necessitated water cooling), the full scale mockup and the configurational mockup as seen in the below graphic. 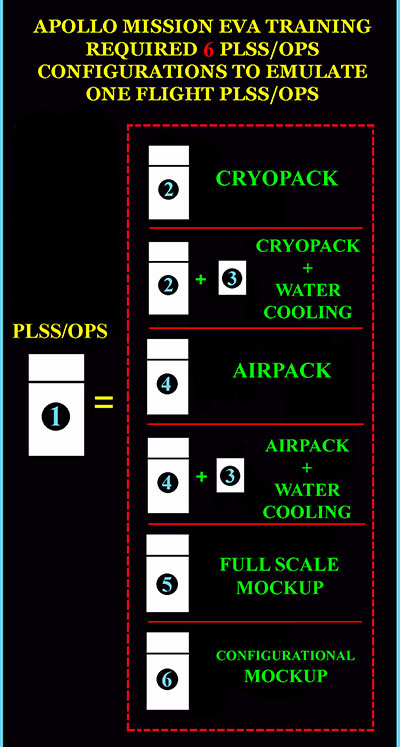 |
Daniel on the Moon Member Posts: 354 From: Bronxville, NY Registered: Jun 2015
|
posted 09-20-2017 02:29 PM
Apollo 11 and Apollo 12 Cryopack Problems and Solutions:The Apollo EVA Crew Training Cryopacks were designed to operate under a nominal heat input of about 1200 BTU/hr. When the heat input dropped below this level the Cryopacks began to accumulate ice in the injector and freeze up, ceasing breathable air flow to the astronaut. This situation limited the external environment the Cryopacks could be used in. Not until we began using the Cryopacks at KSC did we determine the correlation between the designed 1200 BTU/hr heat input, the ambient temperature and the crewman's metabolic work load and more specifically these criteria related to the functional limitations of the Cryopack related to KSC EVA training. With an ambient temperature of below 55°F and a nominal wind velocity, the Cryopack would freeze up. On the other hand, if the ambient temperature was above 80° F, the astronaut metabolic load that the Cryopack was able to dissipate was lower, causing the crewman to sweat profusely during strenuous EVA training exercises on the simulated outside KSC lunar surface. Solving both the Cryopack freeze up problem and the crewman sweating problem resulted in both temporary patchwork solutions and semi - permanent solutions. Both Apollo 11 and Apollo 12 lunar surface EVA Crew Training at KSC was 100% conducted in the KSC Crew Training Building using the Cryopacks. The major problems associated with both Apollo 11 and 12 EVA training exercises was CRYOPACK FREEZE UP AND AIR LEAKAGE. Based on the previously discussed Cryopack design criteria, the Cryopack injectors froze when astronaut metabolic work loads were low (below 1200BTU/hr) and/or when the crew training building temperature was in the low 60's. - CRYOPACK FREEZEUP PROBLEM:
When a Cryopack "froze up" we had TWO OPTIONS. Option one involved using a heat gun to melt the ice in the injector requiring the crewman to be seated until air flow resumed. The nominal Cryopack design use time was 1.5 hr. My decision as PLSS/OPS EVA Crew Training Mission Manager to use or not to use the heat gun was based on the amount of remaining Cryopack functional operational time combined with remaining scheduled training exercise time. - OPTION ONE:
Decision to use the heat gun: As an example, If the total scheduled exercise time was 2.5 hrs and the Cryopack froze at the 30 minute mark with 1 hr remaining on the Cryopack, we used the heat gun to utilize the remaining 1 hour. At the 1.5 hr mark, with no time left on the pack, we switched to a fully charged cryopack to complete the 2.5 hr exercise. As I discussed in a previous post, I had six Cryopacks charged and ready for every crew training exercise (theoretically three for each crew member). - OPTION TWO:
Decision not to use the heat gun: Option two was to replace the disabled Cryopack with another standby pack. As an example, if the Cryopack injector froze at the 1hr mark with only 30 minutes operational use remaining, it did not make sense to stop the training exercise 30 minutes after the previous change. In this case, we changed to a fully charged pack and completed the 2.5 hr exercise. - CRYOPACK AIR LEAKAGE:
As discussed in a previous post, we continually monitored both the Cryopack System Pressure Gauge and the Suit Pressure Gauge. When the system pressure gauge decreased before the Cryopack nominal 1.5 hr operating time, we recognized that we probably had air leakage and immediately notified the test conductor to alert the affected crew member. The affected Cryopack was removed and replaced with a standby pack. By no means were we providing permanent solutions for both the FREEZE UP and AIR LEAKAGE problems. The objective was to successfully accomplish the crew training exercise objectives without having to cancel, potentially compromising the astronaut training schedule which, as we know, had very little or for that matter no time to reschedule, possibly delaying a scheduled launch.As I pointed out in previous posts, it is a "shame" that the training backpacks were not designed with the same quality criteria as was the flight hardware! |
Ronpur Member Posts: 1260 From: Brandon, Fl Registered: May 2012
|
posted 09-20-2017 07:35 PM
I love this!! Great to have you back, Dan! |
Daniel on the Moon Member Posts: 354 From: Bronxville, NY Registered: Jun 2015
|
posted 09-20-2017 09:45 PM
It's great to be back. |
Daniel on the Moon Member Posts: 354 From: Bronxville, NY Registered: Jun 2015
|
posted 09-20-2017 11:28 PM
The following four graphic presentations show both Apollo 11 and Apollo 12 astronauts using cryopacks (as related in my previous post) inside the crew training building.As I also suggested in my previous post, all Apollo 11 and Apollo 12 EVA crew training was accomplished using cryopacks. 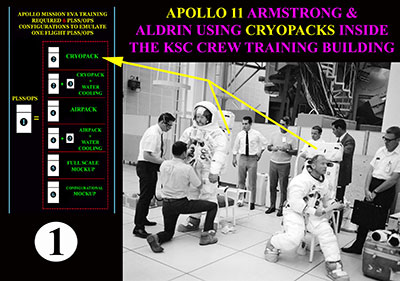 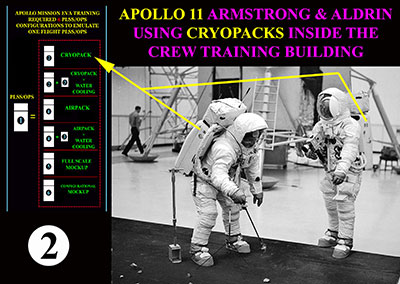
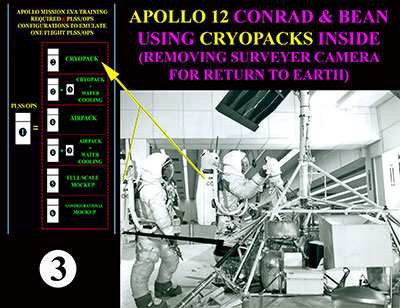
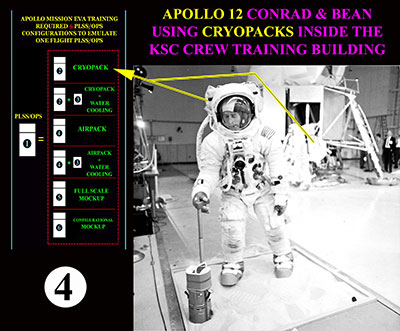
|
Daniel on the Moon Member Posts: 354 From: Bronxville, NY Registered: Jun 2015
|
posted 09-21-2017 01:36 AM
Apollo 13 Cryopack Problems:I'm going to begin this post with the below photo of Apollo 13 LMP Fred Haise that was originally posted by collectSPACE member Rick Mulheirn on 1-15-2016. 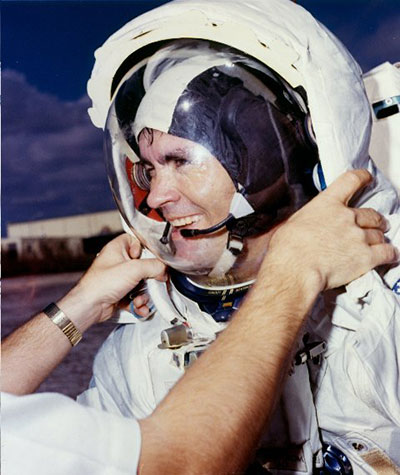 Rick observed that astronaut Haise was sweating profusely as suggested by his sweat soaked comm carrier during a crew training exercise on the KSC simulated outdoor Lunar Surface. Rick asked a logical question: quote: Originally posted by Rick Mulheirn: Given that the temperature of the lunar surface was approximately 170 degrees higher in direct sunlight, what if anything was altered on the suit and the PLSS to compensate for the increased temperatures?
The answer to your question Rick is related to my previous post about the cryopack not being able to dissipate the metabolic heat generated by EVA training outside in the Florida heat when the ambient temperature was above 80°F.Despite the significantly higher temperatures in direct sunlight on the lunar surface, the flight configured PLSS was designed to comfortably cool the astronauts in lunar sunlight. Apollo 13 crew training utilized cryopacks for all EVA training as did the Apollo 11 and 12 astronauts. As with Apollo 11 and 12 crew training inside the KSC crew training building we experienced the identical two major problems, i.e. cryopack freeze up and air leakage. As with Apollo 11 and 12 we implemented the same solutions as previously discussed. In addition to the indoor Apollo 11 and 12 training, Apollo 13 EVA training included outside training on the simulated lunar surface. It was during these outdoor exercises that we discovered the second major cryopack problem, i.e. not being able to dissipate the metabolic heat load generated by the crewman resulting in very uncomfortable significant high suit temperatures as experienced by astronaut Haise sweating in the above posted photo. As many of you know from my past descriptions of the functional aspects of the cryopacks, the cryopacks provided air cooling only. The cryogenic air (liquid air) was converted to breathable air that was also supposed to cool the crewman but, as we know, that was not the case. After the Apollo 13 mission, one sentence in the Apollo 13 final report motivated me to provide a cooling solution for the crewman, i.e. "A training PLSS with a water-cooled loop is badly needed for use in training exercises." |
Rick Mulheirn Member Posts: 4600 From: England Registered: Feb 2001
|
posted 09-21-2017 02:41 PM
Thanks Dan!  |
Paul78zephyr Member Posts: 814 From: Hudson, MA Registered: Jul 2005
|
posted 09-21-2017 09:48 PM
Can you say a few words about Al Worden? I've been so taken by him ever since I read his book and I'd love to hear your opinion of him.(I'm still looking forward to reading your book.) |
Daniel on the Moon Member Posts: 354 From: Bronxville, NY Registered: Jun 2015
|
posted 09-22-2017 12:29 AM
As I mentioned in my last post,the first use of the training PLSS cryopacks outside on the KSC simulated lunar surface was during Apollo 13 EVA training.From a logistics standpoint, we came up with a procedure to transfer the astronauts and equipment to the specific location on the KSC lunar surface that the KSC Crew Systems Division (CSD) test conductor specified for the training run. After we (test conductor, suit techs, cryopack techs and myself) proposed a transfer procedure, I had the opportunity to logistically confirm the procedure. First, we went through the normal suit up procedure that included EMU functional checks and EMU donning (Photo 1). The fully suited crewman stood up and walked out through the back vertical sliding door of the Crew Training Building to a waiting transfer van.The crewmen were each accompanied by both a suit tech and Cryopack tech. While the crewman walked to the van, we transferred the donning chairs and all other equipment for the training exercise to the van and loaded everything through the side doors of the van (Photo 2). Suit pressure was then lowered from 3.7 psi to 1 psi to make it easier for the crewman to sit, legs hanging over the rear bumper (Photo 3),for the ride to the designated lunar surface site (Photo 4). It should be noted that there was enough space for both crewman to ride together on the back of the van as seen in Photo 5. As an aside, after an incident where Al (Shepard) almost slipped off the back of the van, he, in a seemingly angry tone said blaring through the speaker of the hand held comm receiver, "I want to know who's driving and I want to speak with him!" We all knew Al loved to kid around, but being the van driver, I was the target of his fake anger and did not realize he was kidding with me till we stopped and I saw him grinning through his helmet. 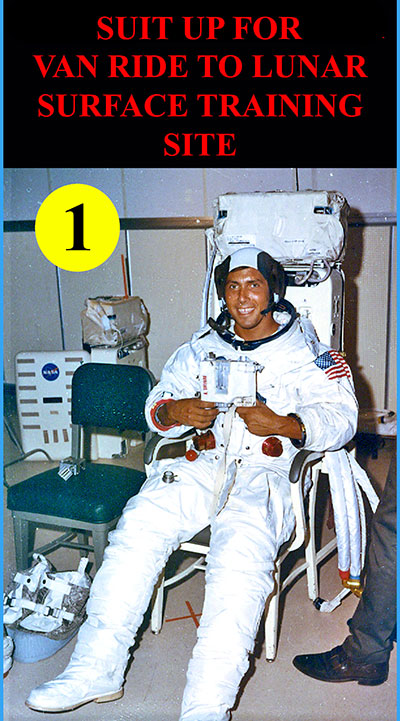 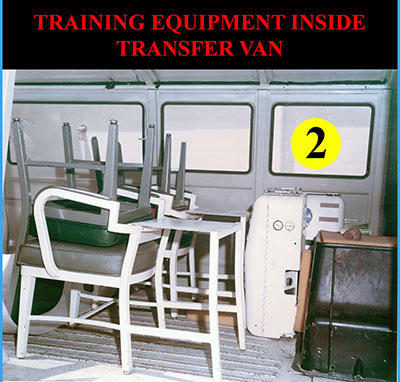
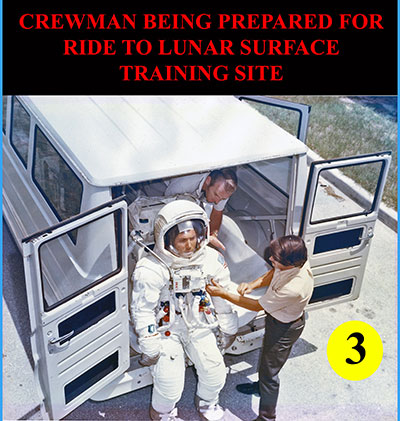
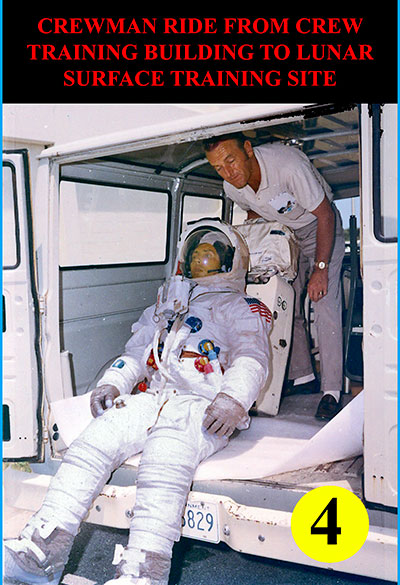
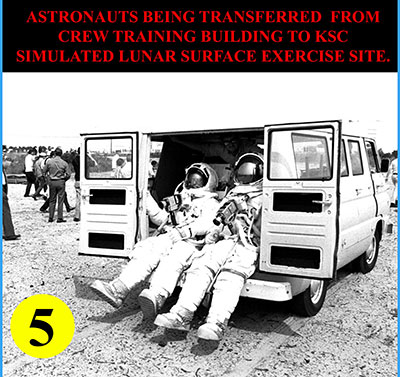
|
Daniel on the Moon Member Posts: 354 From: Bronxville, NY Registered: Jun 2015
|
posted 09-22-2017 01:33 PM
quote: Originally posted by Paul78zephyr: Can you say a few words about Al Worden?
My contact with Al Worden was very brief, basically, to review sim bay EVA cassette retrieval and contingency EVA transfer.I can say that I recall a very humble, attentive and studious approach to information I was conveying. |
LM-12 Member Posts: 4021 From: Ontario, Canada Registered: Oct 2010
|
posted 09-22-2017 02:57 PM
quote: Originally posted by Daniel on the Moon: The fully suited crewman stood up and walked out through the back vertical sliding door of the Crew Training Building to a waiting transfer van.
Was the more familiar crew transfer van considered and then rejected, and where was it kept between missions? |
Daniel on the Moon Member Posts: 354 From: Bronxville, NY Registered: Jun 2015
|
posted 09-22-2017 04:08 PM
The "more familiar" transfer van was used with flight hardware, including flight suits. The van we used was the Hamilton Standard government issued van that did not require a quality control "paper work trail," which was consistent with all our training equipment.Your question reminded me of a crew training exercise that did not begin well at all! For all morning EVA crew training exercises I and my two techs arrived at our HSD building at 6AM to drive our van and pick up the cryopacks at the Bendix facility where the packs were charged with cryogenic air (liquid air). One morning I arrived to find our van had a flat tire. I called and woke up the CSD test conductor (fortunately I had his home phone number) and let him know the situation we were in. He called back about an hour later and said an old NASA van was available and would be driven to our facility for our use. He mentioned that the driver would have to be driven back. Following is a photo of the replacement van and the crew exiting. That's me on the left. 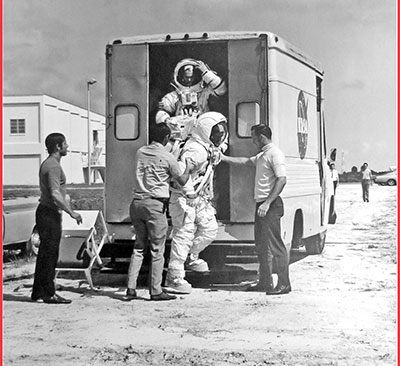 |
LM-12 Member Posts: 4021 From: Ontario, Canada Registered: Oct 2010
|
posted 09-22-2017 06:10 PM
That looks like Cernan and Schmitt. Thanks for the reply, Dan.
|
Daniel on the Moon Member Posts: 354 From: Bronxville, NY Registered: Jun 2015
|
posted 09-22-2017 11:44 PM
Up to this point I talked about Apollo 11, 12 and 13 EVA crew training using the PLSS training cryopacks and the cryopack problems we had, namely, cryopack freeze up, cryopack air leakage and uncomfortable high suit temperatures.After completion of Apollo 13 crew training, we sent the cryopacks to the Manned Spacecraft Center (MSC) in Houston for evaluation and "repair" of both the freeze up and air leakage problem. With repair "modifications" completed the cryopacks were returned to KSC in time for the beginning of Apollo 14 EVA training. Unfortunately, to say the least, we began experiencing the same problems as before with the addition of a new problem, that being unexplained possibly dangerous pressure increases in the cryopack dewar (the cryogenic air reservoir tank) during Apollo 14 crew training runs. This increased pressure climbed higher than the relief valve set at 180psig. The nominal cryopack system operating pressure was 150 psig to 160 psig with the relief valve set at 180 psig. The system pressure was elevating higher than the relief set point resulting in considerable leakage reducing the 1.5 hr nominal cryopack operating time to between 45 minutes and about an hour. My immediate thought was to increase the relief valve pressure and see how high we need to go on the relief valve set point to compensate for the pressure buildup anomaly. The unknown, of course, was how high would the pressure actually increase. We ran a test on all cryopacks with the relief valves removed to see if the pressure buildup stopped increasing beyond 80% of the 300 psig designed proof pressure of the Dewar (240 psig). We found that the maximum pressure, with the relief valve removed, of eight cryopacks tested was 205 psig. We repeated the tests and got similar results. I decided to raise the relief valve pressure to 220 psig. We then tested the cryopacks with the relief valve in the loop and no leakage occurred. I discussed our test results with the dewar manufacturer from a safety standpoint and they agreed that it was reasonable to increase the relief valve setting to 220 psig. We continued with Apollo 14 crew training using cryopacks for both inside and outside exercises. We continued to have the freeze up, air leakage and uncomfortable high suit temperatures. We implemented the same Apollo 11, 12 and 13 solutions. Fortunately we were able to work around the pressure buildup problem with the increased relief valve set point. This was all very disconcerting for me as I felt it was my responsibility to successfully support all EVA crew training exercises. At the same time I was disappointed with MSC sending us "supposed" repaired cryopacks! |
Paul78zephyr Member Posts: 814 From: Hudson, MA Registered: Jul 2005
|
posted 09-23-2017 09:05 PM
quote: Originally posted by Daniel on the Moon: ...I can say that I recall a very humble, attentive and studious approach to information I was conveying.
Dan, thank you for that response about Al Worden. |
Daniel on the Moon Member Posts: 354 From: Bronxville, NY Registered: Jun 2015
|
posted 09-27-2017 09:39 PM
We continued with Apollo 15 crew training using cryopacks for both inside and outside exercises. We continued to have the "freeze up," "air leakage" and "uncomfortable high suit temperature" problems and we implemented the same Apollo 11, 12, 13 and 14 solutions.As I previously stated, my objective as PLSS/OPS EVA Crew Training Mission Manager was to successfully accomplish crew training exercise objectives without having to cancel, potentially compromising the astronaut training schedule which, as we know, had very little or for that matter no time to reschedule, possibly delaying a scheduled launch. Additional cryopack problems were encountered during Apollo 15 Crew Training both inside the Crew Training Building and outside on the simulated lunar surface. Fortunately these additional problems did not affect Crew Training exercises as we always had additional spare charged cryopacks to successfully complete all scheduled exercises. However, more and more time between training exercises had to be devoted to cryopack repair and makeshift modifications. There came a point during Apollo 15 training, when I realized that we had to come up with an alternate PLSS Backpack for training runs to replace the cryopacks, specifically, to eliminate the "freeze up" and "air leakage" problems. After just one problem solving meeting, we agreed that we could modify existing Shell (empty inside) PLSS mockups used for occasions when only an outside dimensionally equivalent flight PLSS envelope was needed. The idea was to utilize the existing Crew Training Building Regulated Air Supply that we were already using to pressurize Astronaut suits and provide breathable air flow during LM suit donning and doffing exercises. During these exercises, the Astronaut wore dimensionally and component correct Hi Fi PLSS/OPS mockups with suit pressurization and breathable air flow supplied from the regulated air supply console directly to the suit inlet oxygen connector and out the suit purge valve. With an unlimited air supply to the crewman, there was no need for re-circulated oxygen and carbon dioxide removal as with the flight PLSS. Modifications to the PLSS shell mockups included adding a regulator, an inlet air hose connector to the back of the shell mockup connected to the regulator. The regulator outlet was a retrofitted PLSS outlet oxygen hose and suit inlet connector. Lastly, we added regulator inlet and outlet (suit pressure) pressure gauges that could be easily visually monitored by any of the support crew. From this point on I will refer to the air regulated shell mockup as the AIR PACK. After fabricating and testing four Air Packs, the next challenge was to figure out how to provide the limited mobility needed inside the Crew Training Building with the crewman's Air Pack air supply hose connected to the stationary air console. The logical answer was to use a long hose. The challenge with a long hose was, how do you walk around the LM conducting EVA tasks without the hose(s) (two crewman) getting snagged on LM projections along the way and preventing the two crewman hoses tangling with each other? The solution we came up with was to construct a "rotating spindle frame" on the top of the Crew Training Building LM Mockup with a radius longer than the furthest LM projection below. The air supply hose from the air regulated console was routed to the center of the rotating spindle frame to rotatable Air Pack hose connectors. I'm providing Graphic 12 below to give you a visual depiction of my written descriptions. 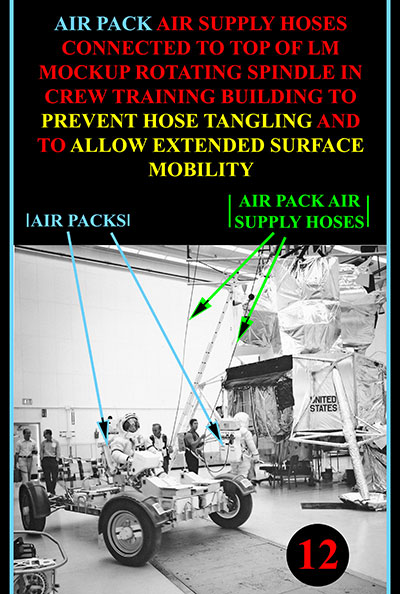 |
Daniel on the Moon Member Posts: 354 From: Bronxville, NY Registered: Jun 2015
|
posted 09-27-2017 11:41 PM
The next challenge was to figure out a way of using the air packs outside on the KSC simulated lunar surface. I made some phone calls and found the availability of a flatbed truck with compressed air cylinders that could be moved to the outside training site.Before celebrating, we asked the next logical question. Can we obtain hoses long enough to support the mobility needed for required training excursions away from the compressed air supply. We were able to coordinate the use of 200 and 300 foot hoses. Graphic 6 below is a pictorial depiction of a crewman wearing an air pack and as can be seen is a considerable distance from the compressed air supply. 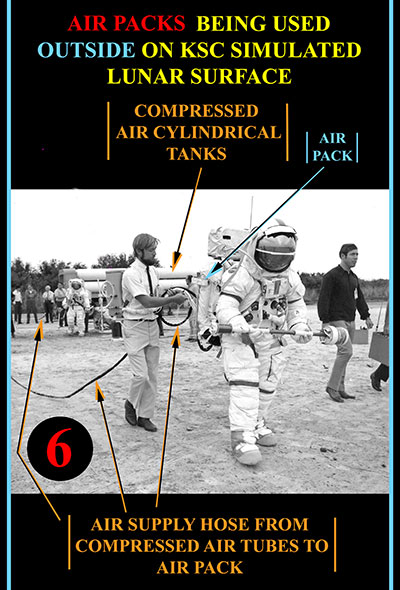 |
heng44 Member Posts: 3774 From: Netherlands Registered: Nov 2001
|
posted 09-28-2017 11:45 AM
quote: Originally posted by LM-12: That looks like Cernan and Schmitt. Thanks for the reply, Dan.
Actually it is Apollo 14 backups Cernan and Engle, September 17, 1970. |
LM-12 Member Posts: 4021 From: Ontario, Canada Registered: Oct 2010
|
posted 09-28-2017 12:58 PM
Okay Ed, Apollo 14. Thanks for the correction. It looks like a similar van can be seen in Apollo 17 photo KSC-72P-438. |
Paul78zephyr Member Posts: 814 From: Hudson, MA Registered: Jul 2005
|
posted 09-28-2017 08:18 PM
Dan, as always thank you for sharing your knowledge and personal history. It is fascinating. Perhaps I am getting ahead of your story but in both pictures 12 and 6, each astronaut seems to be "connected" (via hoses) to a support person that is in turn wearing his own "backpack" of some sort. Can you explain what is going here? Thanks again. |
Daniel on the Moon Member Posts: 354 From: Bronxville, NY Registered: Jun 2015
|
posted 09-28-2017 08:46 PM
You are very observant. The support person backpacks are in fact going to be discussed next in my story. |
Daniel on the Moon Member Posts: 354 From: Bronxville, NY Registered: Jun 2015
|
posted 09-28-2017 10:45 PM
In the back of my mind through both Apollo 14 and Apollo 15 training cycles, I obsessed about the need for EVA "water cooling capability" for EVA training based on the Apollo 13 Final Report that reflected the concerns of Apollo 13 astronauts Lovell and Haise about the uncomfortable high suit temperatures during arduous training exercises both inside and outside the crew training building.My concerned obsession led to a "water cooling pack" depicted in Graphic 7 below. The primary objective was to provide cool water flowing through the crewman's Liquid cooling garment (LCG). As I previously discussed, the cryopack was only capable of supplying breathable air and inadequate crewman air cooling as the cooled cryogenic air flowed from the helmet through the suit and out the open suit purge valve. The flight PLSS as I also previously discussed, had LCG water cooling capability using the process of sublimation only achievable in the vacuum of space. The "Prototype Test Unit" body (A) in graphic 7 was fabricated from molded plastic. It was designed to be carried on the back of tech who became the astronaut's "shadow" as he was connected to the crewman. The hollow interior of the pack (B) was insulated and functioned as a reservoir holding ice and water. The pack had an insulated hinged cover (C) that was opened to add ice (before and during a training exercise) replacing previously added ice that had melted. Different in line water pumps (D) were evaluated for their functional capability of providing a water flow rate of 4lbs/hr through the LCG. When we found an acceptable pump, it was mounted inside the water pack reservoir and connected to the water cooling pack inlet (G) (LCG outlet) and the outlet (H) (LCG inlet). The hose (F) was a lengthened PLSS multiple flow hose (contained both inlet and out flow tubes) including the identical PLSS flight multiple water connector that connected to the suit multiple water connector. The battery (E) hanging off the top rear of the water cooling pack was not the battery that powered the cooling pack pump (D). It was, in fact, the battery that powered the Extravehicular Communications System (EVCS) located inside the training OPS mockup mounted on top of the air pack or cryopack. With the cryopack, the EVCS battery was mounted inside the cryopack but instead of modifying the Air Pack by cutting a hole in the back of the pack and fabricating a battery mounting bracket inside the air pack, I decided it made more sense to mount the EVCS battery on the back of the cooling pack (as depicted in graphic 7) with the battery power cable long enough to reach the EVCS. We found, however, after a number of crew training exercises that the combination weight of the water and ice filled pack plus the weight of the battery was too much to carry during a two to four hour training run. We found it much easier to carry the battery by hooking it on the front or side of the support person's belt. Now that I finished rambling on about the battery (E) that had nothing to do with the water cooling pack, let's get back to the remaining cooling pack features. The space (J) was used to hold the battery that powered the pump (D). The last component was a drain tube (I) that was used to drain melted ice water to make room for additional ice during a training run. 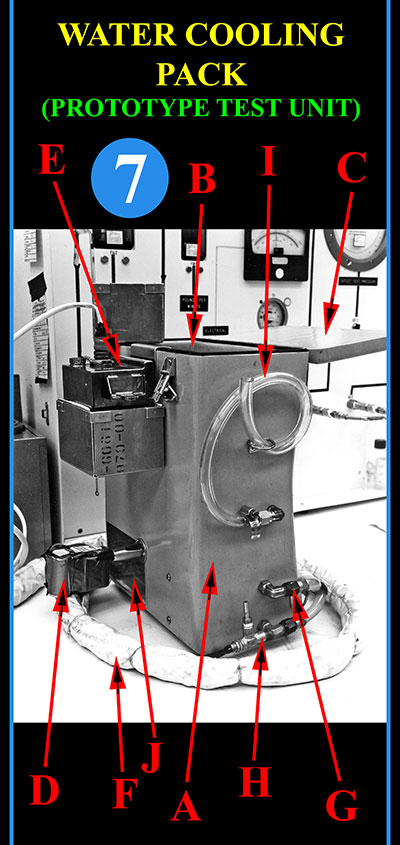 |
Daniel on the Moon Member Posts: 354 From: Bronxville, NY Registered: Jun 2015
|
posted 09-29-2017 05:33 PM
We began using the aforementioned "water cooling packs" at the start of Apollo 16 EVA training.Following are three graphic representations showing the water cooling packs and also the previously discussed "Air Packs" being used during both inside and outside crew training exercises: 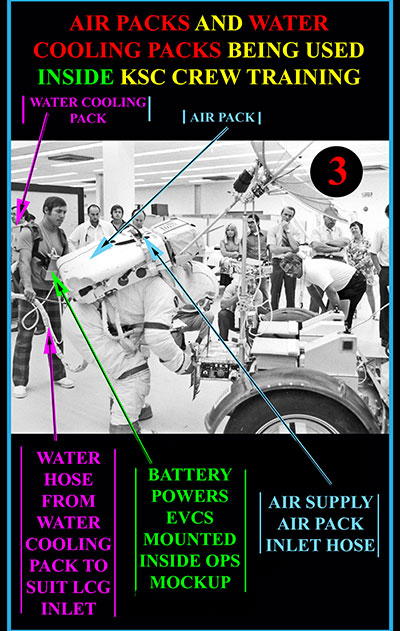 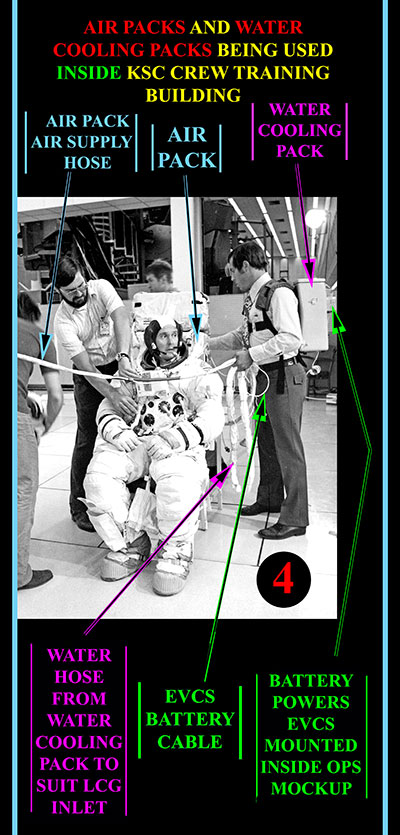
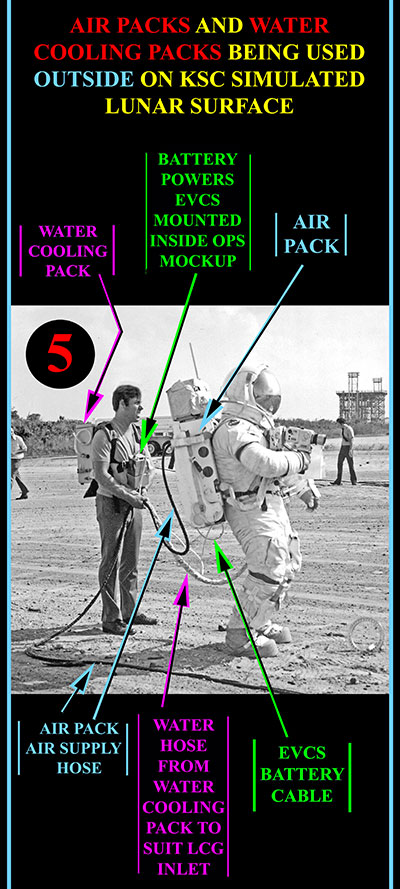
|
Daniel on the Moon Member Posts: 354 From: Bronxville, NY Registered: Jun 2015
|
posted 09-29-2017 11:06 PM
In Graphic 8 below, one of my techs is preparing a "water cooling pack" for use.The hinged cover of the water cooling pack (A) is about to be opened by a technician so that he can add water from the bucket (C) to about 1/3 volume of the cooling pack reservoir. The tech will then fill the bucket with ice cubes from one of the two styrofoam ice chests (B). The tech will then add ice to the cooling pack to a level about 1" from the top of the pack. Prior to the crewman standing, the tech, with the help of another support crew member, will mount the water cooling pack on his back. Note the cooling pack has cushioned support harness straps (D). When the crewman is completely suited with helmet on and pressurized, the tech will connect the Cooling Pack water hose (E) to the crewman's multiple water connector. Lastly, someone other than the tech carrying the cooling pack will turn the cooling pack pump toggle to the on position. The location of the pump toggle switch is hidden in graphic 8 below. I will locate the toggle visually in a future graphic. 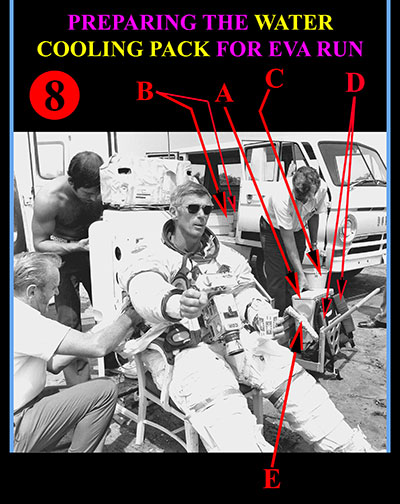 |
Daniel on the Moon Member Posts: 354 From: Bronxville, NY Registered: Jun 2015
|
posted 09-29-2017 11:25 PM
In my previous post, Graphic 8 did allow me to point out the water cooling pack pump on/off toggle switch. In the below Graphic 9 I've identified the location of the cooling pack pump battery in the rear lower left open compartment. You can also see the battery power cable routed to the pump inside through the rear wall of the cooling pack reservoir. The pump on/off toggle switch cannot be clearly seen, however, it is in line with the battery cable.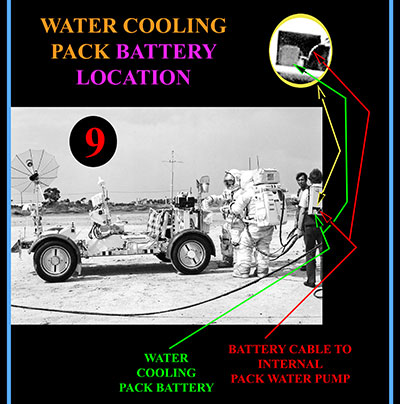 |
Daniel on the Moon Member Posts: 354 From: Bronxville, NY Registered: Jun 2015
|
posted 09-30-2017 12:16 AM
The "water cooling pack" was a solution to the uncomfortable high temperatures that the astronauts experienced during Apollo 11, 12, 13, 14 and 15 EVA training.Granted, it was a "makeshift" solution, but the bottom line is that it worked, i.e. it keep the crewman cool by circulating cooled water through the crewman's Liquid Cooled Garment (LCG) rather than the non-existent cooling capability of the cryopack. Referring to Graphic 10 below, the water cooling pack had to monitored and "serviced" during the EVA run, runs that sometimes lasted more than four hours. In Graphic 10, a tech is draining melted ice water from the cooling pack (A) into the bucket (B) without interrupting the training exercise. The water was then emptied to one-third pack volume level. The tech spilled the water out of the bucket and filled the bucket with ice cubes from one of the two ice chests waiting nearby. The ice was then added to the pack reservoir. Draining cooling pack water and adding ice cubes continued for the duration of the training run. The number of times necessary to "service" the cooling pack was, of course, determined by both the ambient temperature and the crewman's metabolic work load. 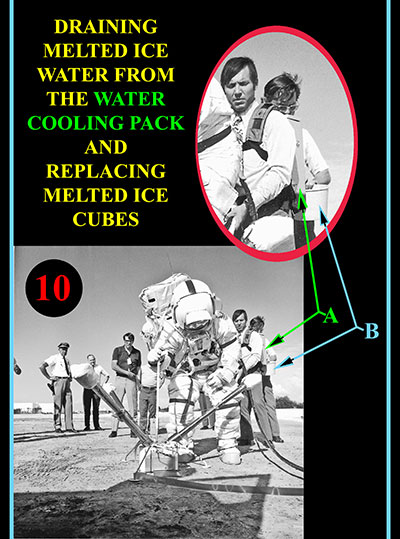 |
Daniel on the Moon Member Posts: 354 From: Bronxville, NY Registered: Jun 2015
|
posted 09-30-2017 10:36 AM
I bet you thought we were finally able to "deep six" the cryopacks. No such luck! As logic would have it, EVA training for Apollo 16 and 17, when the airpacks and water cooling packs were available, could not be used when lunar rover excursions on the simulated lunar surface were necessary, as tethering anything (airpack and/or water pack hose) to the crewman riding on the rover was not an option (Graphic 11 below).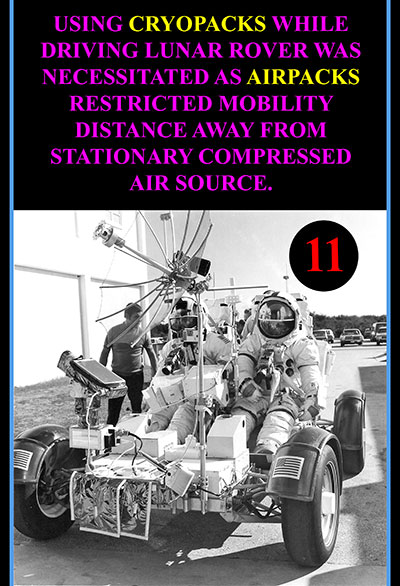 |
Blackarrow Member Posts: 3775 From: Belfast, United Kingdom Registered: Feb 2002
|
posted 09-30-2017 11:26 AM
quote: Originally posted by Daniel on the Moon: My contact with Al Worden was very brief, basically, to review sim bay EVA cassette retrieval and contingency EVA transfer.
Were your contacts with Ken Mattingly and Ron Evans similarly brief? |
Daniel on the Moon Member Posts: 354 From: Bronxville, NY Registered: Jun 2015
|
posted 09-30-2017 01:06 PM
My contact with Mattingly was more extensive from a working relationship than my "brief" working time with Worden as Ken Mattingly was assigned to follow EMU development and implementation. In that role, he was responsible for proposing and evaluating PLSS/OPS and suit modifications. Ken's responsibility included being the liaison between EMU contractors, NASA Crew Systems Division (CSD) and his fellow astronauts.I worked with Ken coordinating his comments and proposed changes related to the PLSS/OPS. Ken was dedicated and a very important and influential voice during PLSS/OPS development. He apparently enjoyed his work with PLSS development as evidenced in his comments to me in the below photo, i.e. "Best wishes to Dan, you folks have done an outstanding job. I thoroughly enjoyed my work with the PLSS development." 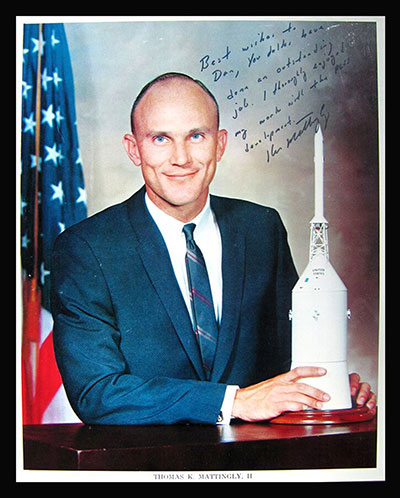 My contact with astronaut Evans with respect to work with the PLSS/OPS was similarly as brief as that with Al Wordon. However, contact with Ron was quite extensive from a social standpoint as evidenced from the party photos at my apartment. He was a "fun loving guy!" 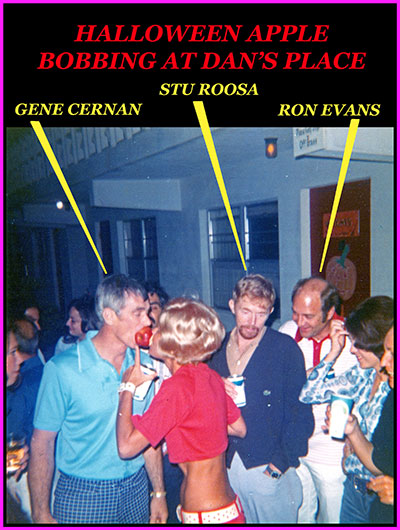 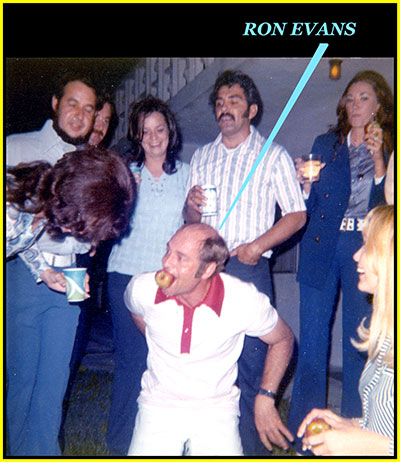
|
Daniel on the Moon Member Posts: 354 From: Bronxville, NY Registered: Jun 2015
|
posted 09-30-2017 02:05 PM
There were a considerable number of Apollo 16 and 17 EVA crew training runs that required the use of both cryopacks and airpacks/water cooling packs.Referring to the below Graphic 13, as can be seen in the photo, the crew training run was scheduled for both lunar rover excursions and stationary experiment deployment and/or rock sampling. In the photo, the suited crewman is wearing a cryopack and is going to walk over to and "board" the lunar rover for un-tethered rover excursions (if and when he stops flirting with the young lady sitting in the passenger seat of the jeep!). After completing the scheduled rover tasks, the crewman will exit the rover and walk to the cryopack/airpack donning/doffing chair(s). The cryopack will be removed, the crewman will drink Gatorade, he will don the airpack and connect to the airpack supply hose seen in the photo. With the airpack supply hose connected, he will execute the scheduled EVA timeline "stationary" objectives. I should mention that, on a very hot day as it was on the day the below photo was taken, I connected the water cooling pack to the crewman during his walk and standup tasks around the rover before boarding the rover. 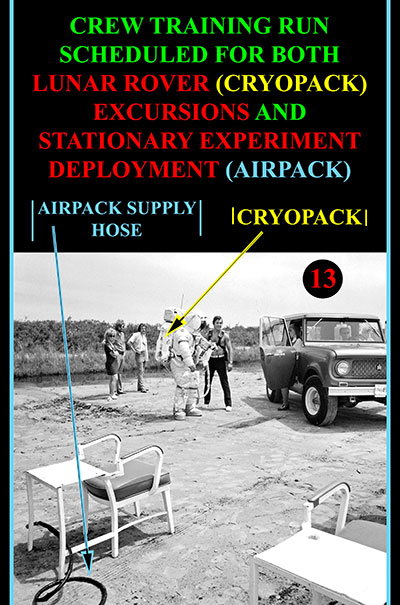 |
Daniel on the Moon Member Posts: 354 From: Bronxville, NY Registered: Jun 2015
|
posted 09-30-2017 09:33 PM
Graphic 14 below includes a description of an Apollo 16 EVA training exercise and a map of the simulated KSC lunar surface.A day before each EVA training exercise, I was given both a "menu" (A) defining for me what equipment we would have to prepare to support the exercise. Along with the "menu", a map (B) was included if the exercise involved mobility utilizing the lunar rover. Referencing menu (A), at 08:00 we attended a pre-brief meeting and then crew suit up. At 08:30, an EVA 2 exercise was initiated inside the crew training building utilizing airpacks. At 09:00 airpacks were removed and cryopacks were donned for a lunar rover (LRV) drive from the crew training building to Station 8 identified on Map (B). Next was an LRV drive to Station 17 (Map B). Next was an LRV drive to Station 4. Each time the crew arrived at a station, water cooling packs were connected while the crewman practiced defined stationary station procedures. As you can see in Menu (A), training time was 3.5 hrs. The last item on the menu, i.e. "Secure or EVA 2 Closeout" was dependent on the crew schedule that day. What it usually meant was whether or not the crewmen were "up for" changing back to airpacks and going through the EVA 2 closeout procedures which added another 1.5 hours! 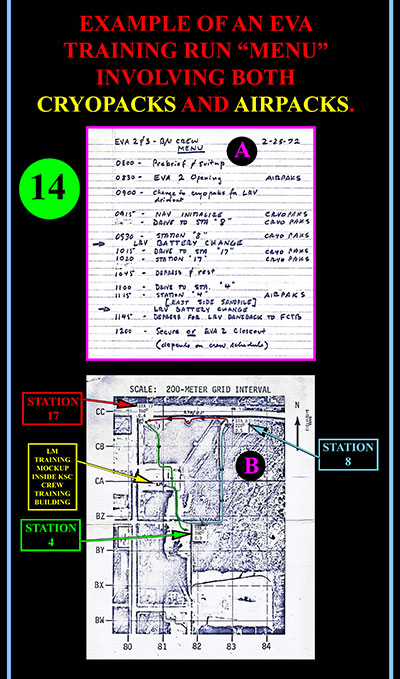 |
mikepf Member Posts: 448 From: San Jose, California, USA Registered: Mar 2002
|
posted 10-02-2017 05:33 PM
Dan, I don't have any specific questions formulated at this time, but I wanted to check in and let you know that I am following your posts with great interest. Please keep up your documentation of your part of the training process. This is all part of the story that hasn't been told yet as far as I am aware. |
Daniel on the Moon Member Posts: 354 From: Bronxville, NY Registered: Jun 2015
|
posted 10-02-2017 06:48 PM
Thank you Mike for your interest. I will try to do my best conveying my Apollo experiences. There may be days or possible weeks between posts however, you can be assured that there will be a continuation of future posts. |
LM-12 Member Posts: 4021 From: Ontario, Canada Registered: Oct 2010
|
posted 10-02-2017 09:05 PM
Up until now, I did not know that the LRV training area also went north of the Flight Crew Training Building. Thanks for the map. |
Daniel on the Moon Member Posts: 354 From: Bronxville, NY Registered: Jun 2015
|
posted 10-02-2017 09:55 PM

|
Daniel on the Moon Member Posts: 354 From: Bronxville, NY Registered: Jun 2015
|
posted 10-02-2017 11:23 PM
I've been discussing the different PLSS/OPS hardware configurations that were necessary to emulate the only "ONE" flight configuration PLSS/OPS necessary to support Apollo KSC EVA Crew Training.The below graphic blue check marks represent hardware training configurations and combinations that I've discussed in previous posts, i.e. Cryopack, Cryopack + Water Cooling Pack, Airpack and the Airpack + Water Cooling Pack. When discussing the aforementioned configurations, I tried to give you enough detail to understand the story and rationale behind the need for these multiple training Life Support hardware. In future posts I will discuss the need and use of PLSS/OPS Full Scale Mockups and Configurational Mockups. Stay Tuned! 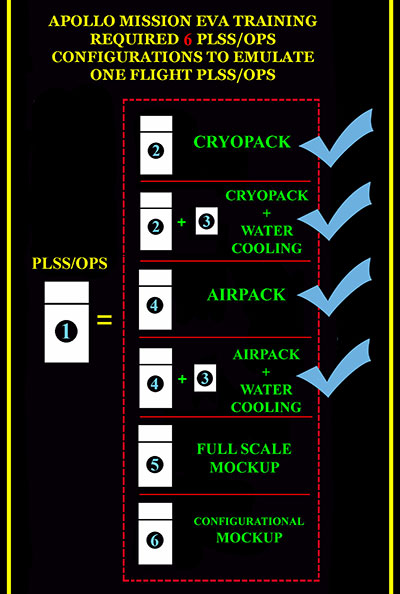 |
Daniel on the Moon Member Posts: 354 From: Bronxville, NY Registered: Jun 2015
|
posted 10-03-2017 11:16 PM
The previously discussed cryopacks, airpacks and water cooling packs were all used for astronaut life support during lunar surface EVA training. They provided the suited crewman with breathable air, suit pressurization and eventually water cooling.Not only did the Apollo CDR and LMP spend a great deal of training preparing for Lunar surface activities, they spent many hours training for donning (EVA Prep) and doffing (EVA Post) their EMU (Suit and PLSS/OPS) preparing for LM exit and LM return. The procedures for LM EVA Prep and Post necessitated the use of full scale PLSS, OPS and remote control units (RCU) as these procedures specifically related to preparing the PLSS, OPS and RCU for donning and doffing. The specific procedures were documented on EVA pre and post "cue cards" that were secured by a clip in a fixed visible vertical position in the LM so that the crewmen could read each procedural step as they worked their way through the procedures. In the below Graphics A, B and C, I related examples of cue card written procedures to actual pictorial representations of crewman performing the procedures. When the crewman went through the EVA prep and post procedure, the objective was "practicing to learn." I had the incredible opportunity to perform the same prep and post procedures with the following objectives: - Verify written procedural steps successfully accomplished objectives.
- Determine if procedural steps should or could be modified from a "human factors" standpoint.
- Evaluate requested crew procedural changes and possible hardware modifications for evaluation.
One of my responsibilities at KSC was to make sure the crew training PLSS, OPS and RCU mockups were identical to the flight hardware. This involved keeping track of all changes made to the flight PLSS, OPS and RCU and updating the mockups when necessary.Each time a change was made to the flight hardware that involved astronaut PLSS, OPS or RCU procedures, inspection, component change briefings, etc., I was responsible for implementing the change to the mockups keeping in mind that the astronauts use of the flight hardware was based on their training with the mockups. Imagine, for instance, if a configuration change was made to the flight hardware and was not implemented in the mockups and subsequently not recognized by the crew on the moon, there might have been disastrous consequences. 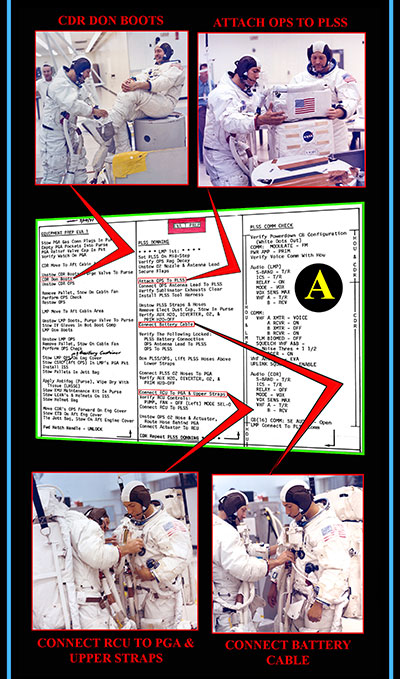 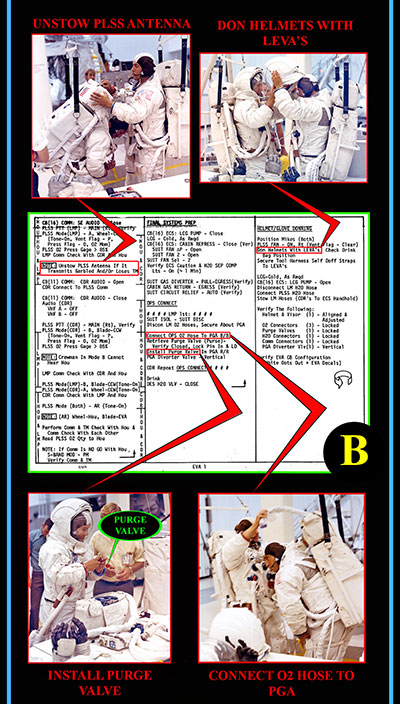
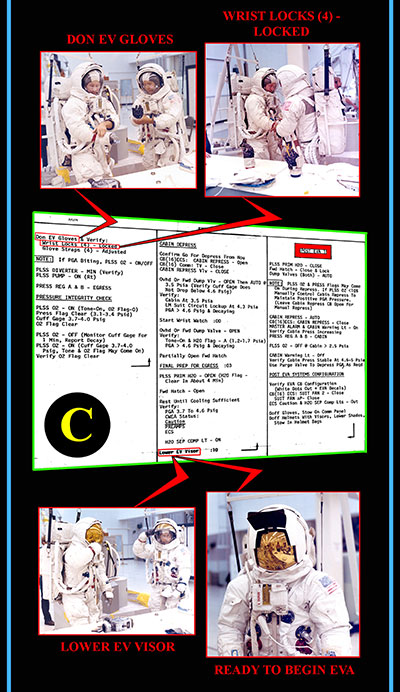
|
MCroft04 Member Posts: 1861 From: Smithfield, Me, USA Registered: Mar 2005
|
posted 10-04-2017 01:56 PM
Were there procedures to insure that changes to flight hardware were quickly communicated to you? If so, were the procedures followed adequately? Did you ever receive feedback from an astronaut that their final flight hardware (when they reached the moon) was different from the training hardware? Seems like a lot of room for something to go wrong. |